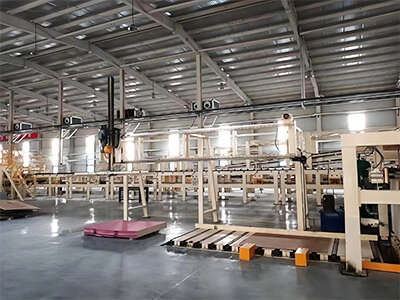
Gypsum Board Machine Factory
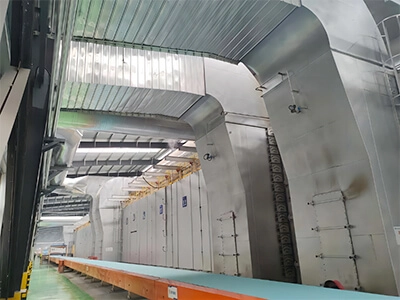
Paper Faced Gypsum Board Machinery
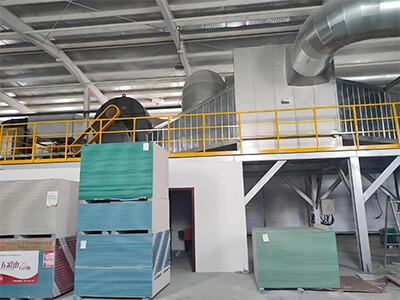
Produce Gypsum Board
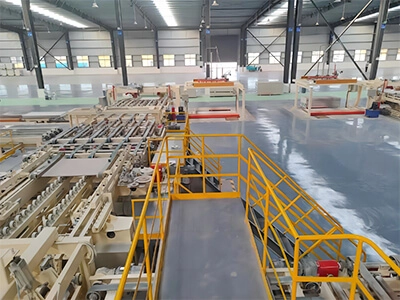
Paper Faced Gypsum Board Production Line
The blessings of this approach are excessive yield, excessive frying efficiency, speedy solidification of the got Plaster, low strength, however complicated equipment.
First, crush the Plaster into nice sand particles, then stir fry it, and then crush and display it.
Use a widespread squirrel cage crusher to crush, select, and screen. The benefit of this approach is that it has the benefits of the first two methods, however the manner is fantastically complex.
This technique is nonetheless broadly used in the home ceramic industry.
Pressure steaming approach for frying paste
This approach first preheats the uncooked Plaster with a block dimension of 25-50mm after coarse crushing in warm air at 60 ℃, and then locations it in a stress cooker for 5-7 hours with saturated superheated steam at 1,3 atmospheric strain (125 ℃). Then, warm dry gasoline at 200 ℃ is added till warm dry fuel is discharged, ensuing in a vapor stress of hemihydrate Plaster. This kind of hemihydrate Plaster is in the A-crystal form, and the power of the mannequin flipped with this kind of hemihydrate Plaster is very high, however the gear for this frying approach is greater complex.
Regardless of the method, the fineness of Plaster powder commonly requires a residue of no extra than 0.5% on the 80-120 mesh sieve.
Five principal structures of constructing Plaster powder manufacturing line
According to the procedure requirements, the building Plaster manufacturing line is commonly divided into 5 parts, specifically the crushing system, grinding system, calcination system, storage and transportation system, and electrical manipulate device.