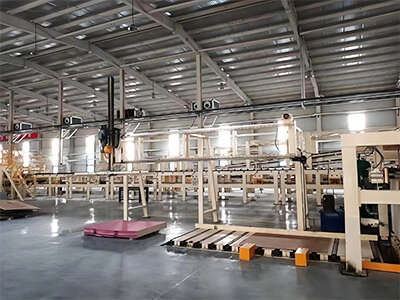
Gypsum Board Machine Factory
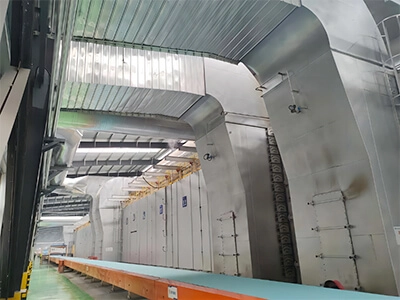
Paper Faced Gypsum Board Machinery
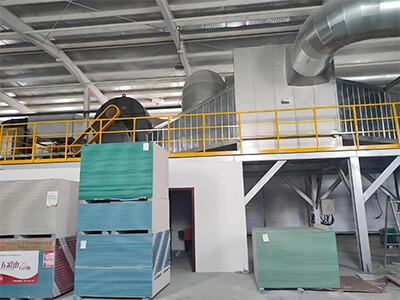
Produce Gypsum Board
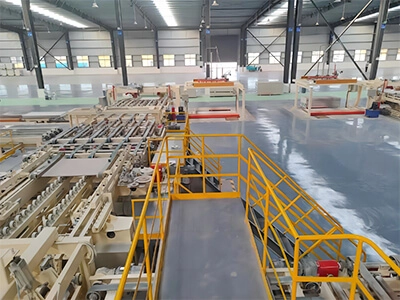
Paper Faced Gypsum Board Production Line
Material conveying
The beaten Plaster uncooked fabric is transported via a hoist to a storage bin for backup. The storage bin is designed in accordance to the necessities for fabric storage time to make sure a steady provide of materials. At the equal time, elevators are used for cloth turnover in quite a number components to decrease the ground area.
Plastering MachineProcessing technology
Phase 1: Crushing
The giant Plaster is overwhelmed through a crusher to a feed fineness of 15mm-50mm that can enter the grinding machine.
Phase 2: Grinding
The beaten small portions of Plaster are despatched to the silo via a hoist, and then evenly and quantitatively fed into the grinding chamber of the grinding desktop for grinding via a vibrating feeder.
Stage 3: Grading
The Plaster powder after grinding is graded by way of a powder concentrator, and the unqualified powder is graded by means of the powder concentrator and again to the mill host for re grinding.
Stage 4: Powder Collection
The Plaster powder that meets the fineness necessities flows via the pipeline and enters the dirt collector for separation and collection. The accrued completed powder is transported to the completed cloth warehouse thru the discharge port with the aid of a conveying device, and then packaged uniformly the usage of a powder loading tanker or an automated packaging machine.
Plaster, additionally recognized as fine-grained stone, is a hydrate of calcium sulfate, which is white or colorless and transparent. Natural Plaster is non-toxic, harmless, and non corrosive to the human body. It is generally overwhelmed and floor into Plaster powder and is broadly used in a number industries. Next, I will provide you a specified introduction to the Plaster grinding process.