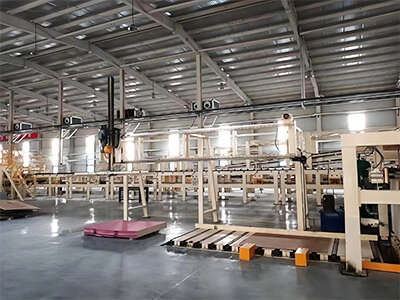
Gypsum Board Machine Factory
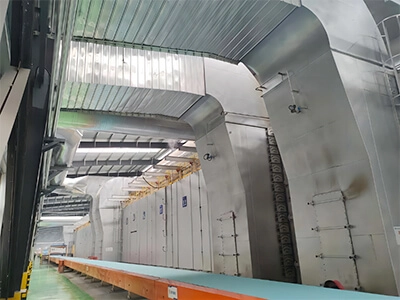
Paper Faced Gypsum Board Machinery
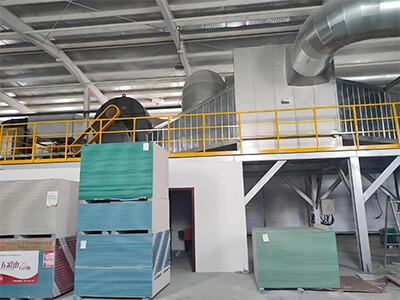
Produce Gypsum Board
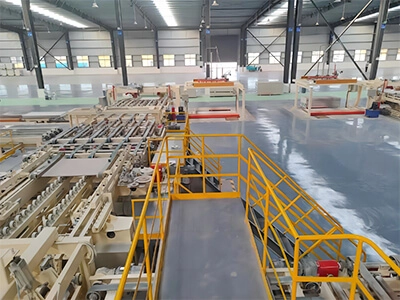
Paper Faced Gypsum Board Production Line
Crushing system:
The plaster raw material enters the crusher through a feeder, which crushes large-sized plaster ore into small particles smaller than 30mm for backup. According to the size of plaster raw materials and different production requirements, corresponding specifications of crushers can be selected, usually PE jaw crushers, PC hammer crushers, or PF impact crushers. In order to protect the clean environment, dust removal equipment can be equipped to meet environmental emission requirements.
Grinding system:
The plaster raw substances in the storage bin are fed into the grinding desktop thru a vibrating feeder for precision processing. An electromagnetic vibration feeder is set up underneath the storage bin, which is interlocked with the mill to regulate the provide of substances in real-time based totally on the operation of the mill.The material is uniformly and persistently fed into the mill through an electromagnetic vibration feeder for grinding. The plaster raw powder after grinding is blown out via way of the airflow from the mill blower and categorised by way of way of the assessment laptop computer above the predominant machine.
The powder with the specified fineness enters the large cyclone collector with the airflow, and is collected and discharged through the powder discharge pipe to form the finished product. The finished product falls into the screw conveyor and is transported to the next system for calcination. The airflow flows into the blower through the return air duct of the large cyclone collector. The entire air duct system is closed loop and flows under negative pressure. Due to the presence of water in the ground raw material and its evaporation into gas during the grinding process, the air volume in the circulating air path increases. This increased air volume is introduced into the bag filter through the pipeline between the cyclone collector and the blower to remove dust from the air and discharge it into the environment to ensure cleanliness. The material passing through the grinding system has been changed from a particle size of 0-30mm to 80-120 mesh, which meets the fineness requirements of plaster powder.